PU foam stress ball release agents help improve production efficiency by stopping foam from sticking to molds, cutting down on mold cleaning time, and making it easier to remove parts. If you’re making PU foam balls, release agents help you make more parts faster because the foam doesn’t stick to the mold. You don’t have to stop and clean the mold as often, and you can get the parts out easier. Release agents work by forming a thin, non-reactive film on the mold. This lets you make parts faster and with better quality, so you have fewer defects and less downtime. You need to use the right release agent for your PU foam material and mold to get the best results.
In the manufacturing world, the right release agent can make all the difference. This is especially true for PU foam stress balls, which require precise and efficient production processes to meet high-quality standards. In this article, we’ll explore everything you need to know about PU foam ball release agents, including their types, uses, and best practices. Our aim is to give B2B buyers the information they need to make smart purchasing decisions and achieve the best production results.
What is a Polyurethane Release Agent?
Polyurethane release agents are coatings applied to the surface of molds to form a layer with low surface tension, making the mold surface smooth and highly non-stick. This reduces the adhesion between the mold and the material inside it, allowing the finished product to be easily removed from the mold. This enhances efficiency and simplifies the manufacturing process. Typically, polyurethane release agents are made from a mixture of polyurethane resin, plasticizers, lubricants, and solvents, offering excellent chemical resistance and wear resistance.
Polyurethane release agents can be applied to various materials such as PU foam sheets, rubber, plastic, and composites, and they are widely used in the manufacturing processes of industries including automotive, aerospace, medical devices, electronics, and toys.
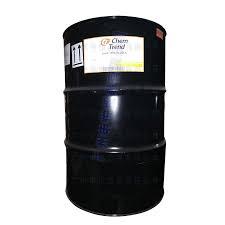
Why Use Release Agents?
Release agents are a must for making Polyurethane foam products, especially when you’re molding foam. They help you get the parts out of the mold quickly and easily, so you can make more parts faster and with fewer defects. If you didn’t use a release agent, the material would stick to the mold, and you’d have to stop and clean the mold, which would slow you down and increase the chances of damaging the parts.
1. Background
Polyurethane (PU) exhibits excellent adhesion to other materials, which is bad in foam molding. During the production of molded PU foam, cast polyurethane elastomers, and rapidly developing reaction injection molding (RIM) products, release agents are necessary for the swift and smooth removal of products from molds.
2. Main Functions
PU release agents are special agents in the production process of PU foam products. During the development of release agents, there are several factors including the type of PU foam formulation, processing temperature, machinery used, processing cycle time, product style, and mold design.
The first function of PU release agents is to form a uniform release film on the mold surface, enabling easy removal of the molded products. The second function is to ensure the quality and style of the molded product’s surface, the feasibility of cleaning mold deposits, and the applicability of subsequent treatments. Other factors to consider include the product’s shelf life, stability, health or safety concerns for users and manufacturers, and corrosion issues.
- Create a thin, even layer on the mold surface that the part won’t stick to
- Give you a good surface finish on the part
- Keep the mold clean
- Make it easy to clean the mold
- Not mess up the part
Release Principles
PU (polyurethane) release agents reduce the bonding force between polyurethane and the mold surface, typically due to two factors. First, mold surfaces are often covered with a thin water film, which reacts with isocyanates to create strong adhesion. Second, adhesion is due to chemical bonds formed by the interaction between polar groups on the mold’s surface and the polyurethane and polyol’s polar groups.
To achieve good release, a dense, smooth film must be formed on the mold surface, which does not react with raw materials yet adheres well to the mold and is flexible. Effective release substances (usually inert) are uniformly sprayed onto the mold via a medium (water) and form a smooth film. After the medium evaporates, you get a smooth film that achieves the release effect.
Types of PU Foam Stress Balls Release Agents
Polyurethane release agents are classified into external and internal release agents. Most polyurethane product manufacturers in China use external release agents. Internal release agents are part of the foam formulation. They change the foam formula and affect the physical properties of the product. Therefore, external release agents are widely used and continuously developed. In this article, we focus on external release agents.
1. External Release Agents
External release agents are applied directly to the mold surface before each production cycle. They form an inert film that prevents the PU foam from sticking to the mold.
They are classified based on usage:
- Durable type: Applied once, it can mold multiple times.
- Regular application type: Applied before each molding.
- Multi-layer composite type: Regularly used type with various compounds.
The most commonly used type is the regular application type, and these external release agents can be further classified based on the types of compounds used. PU foam manufacturers often choose the regular application type, especially for products like PU balls.
Types of External Release Agents
- Silicone-Based Release Agents:
- Solvent-based (silicone oil, silicone paint)
- Emulsion-based (silicone oil)
- Compounds (silicone oil silica)
- Aerosol (silicone oil)
- Drying (cross-linked silicone)
- Silicone-based release agents are widely used due to their low surface tension, heat resistance, non-toxicity, good gloss, and non-reactivity with resins.
- Silicone-based release agents generally have good release properties and don’t contaminate the molds.
- They’re often used in high-density polyurethane foam production and for producing foam products like PU foam sheets and PU foam spray.
- Wax-Based Release Agents:
- Natural wax (carnauba wax)
- mineral wax (FT wax)
- Synthetic wax (polyethylene wax)
- Wax-based release agents have good adhesion and post-processing properties, and they are cost-effective.
- They are widely used as release agents for polyurethane foam production processes. However, these release agents cause significant contamination to the mold, requiring frequent cleaning.
- Grease-Based Release Agents:
- Animal grease (whale oil)
- petroleum grease (petroleum jelly)
- Grease-release agents like petroleum jelly are low-cost and simple but can leave oily residues on product surfaces.
- They are less commonly used for polyurethane balls due to these drawbacks.
- Fluorine-Based Release Agents:
- Perfluoroalkyl compounds (solvent-based, water-based, aerosol)
- Perfluoroalkyl acrylate
- Fluororesin powder (low molecular weight PTFE)
- Fluororesin coating (PTFE, FEP, PFA)
- These release agents are often chosen for high-performance applications, including high-density polyurethane foam production, offering superior durability and minimal contamination.
- Inorganic-Based Release Agents:
- Solid agents like talcum powder, mica, and clay, require suitable formulations for use.
- Surfactant-Based Release Agents:
- Rarely used alone but often combined with other components.
- Fluorine-Based Release Agents:
- Fluorine-based release agents have good release properties and cause minimal contamination to the mold. However, the cost of these release agents is relatively high, which limits their usage to some extent.
- Other Types of External Release Agents:
- Other types of external release agents include resin-based release agents, primarily made of polyethylene and polypropylene. Additionally, there are phosphates and shellac.
Comparison of Release Agent Types
Type | Application Frequency | Cost | Durability | Mold Cleaning Frequency |
---|---|---|---|---|
Silicone-Based Release Agents | Regular | Medium | High | Low |
Wax-Based Release Agents | Frequent | Low | Medium | High |
Grease-Based Release Agents | Regular | Low | Low | Medium |
Fluorine-Based Release Agents | Regular | High | High | Low |
Inorganic-Based Release Agents | Varies | Medium | Medium | Medium |
Surfactant-Based Release Agents | Rare | Medium | Low | Medium |
Fluorine-Based Release Agents | Regular | High | High | Low |
Other Types of External Release Agents | Regular | Medium | Medium | Medium |
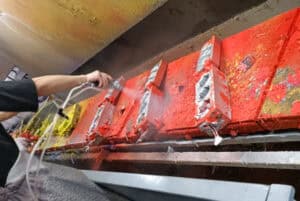
2. Internal Release Agents
Internal release agents are added to PU foam formulations. They migrate to the foam-mold interface to achieve the release effect. They are widely used in high-tech industries like automotive and are particularly beneficial in high-volume PU foam production processes. Widely used in the automotive industry in the U.S. and Europe.
Key Features of Effective Release Agents
To ensure smooth-surfaced products, release agents must have the following characteristics:
- Good thermal and chemical stability, without reacting with the PU foam material.
- Excellent release properties, forming uniform thin films and accurate, complex shapes.
- Non-corrosive to molds, leaving no residue or decomposed material on the mold surface, and not contaminating parts.
- Smooth product surfaces, preventing dust adherence due to the release agent.
- Superior secondary processing performance, not affecting post-processing such as painting, printing, and bonding.
- Minimal mold cleaning time.
- Non-toxic, safe, and easy to use.
- Low cost.
Application Methods
1.Spray Application
Spray application is the most common method for external release agents. It ensures a uniform coating and is suitable for PU foam production processes.
2. Wipe Application
Wipe application is when you take a cloth or sponge and put the release agent on it. You then wipe the release agent on the mold. This is good for PU foam molding process.
3. Dip Application
Dip the mold in the release agent. It’s efficient for big qty production but may require more cleanup. This is good for high-volume production, especially when working with complex PU foam making formulas, but you may have to clean up more.
Industry-Specific Applications
Automotive Industry
- PU Foam Seat Cushions: Release agents ensure the smooth production of foam seat cushions, critical for comfort and safety.
- Headrests and Armrests: Maintain the shape and surface quality of these components.
Toy Industry
- PU Foam Stress Balls and other Foam Toys: Ensure consistent quality and easy removal from molds to meet safety standards and aesthetic requirements.
Medical Industry
- Orthopedic Supports: Provide precise shaping and smooth surfaces for comfort and functionality, which rely on effective polyurethane foam materials.
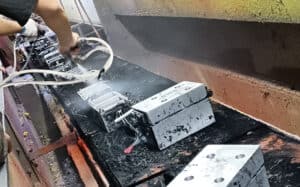
Choosing the Right Release Agent
Selecting the appropriate release agent depends on several factors, including:
- Type of PU Foam: Different types of foams, like high-density polyurethane foam, may require specific release agents.
- Production Volume: High-volume production may benefit from durable, multi-cycle release agents.
- Mold Material: Compatibility with the mold material ensures better performance and longevity.
- End-Product Requirements: Surface finish, post-processing needs, and regulatory compliance are crucial considerations.
Decision-Making Table
Factor | Consideration | Recommended Release Agent Type |
---|---|---|
PU Foam Type | High rebound, slow rebound, integral skin | Silicone-Based, Wax-Based |
Production Volume | High or low order qty | Silicone-Based, Fluorine-Based |
Mold Material | Aluminum, steel, composite | Silicone-Based, Fluorine-Based, Wax-Based |
Surface Finish | Smooth, textured | Silicone-Based, Wax-Based, Fluorine Release Agents |
Regulatory Compliance | Safety and environmental regulations | Silicone-Based, Inorganic, Surfactant-Based, Fluorine-Based |
Conclusion:
In our PU foam stress ball industry, the release agents we use depend on the surface we want. Most of the time, we use semi-oil semi-wax release agents. Sometimes, we use full-wax release agents. The engineers will decide which one to use based on the stress ball surface that the customer wants.
Please let me know without hesitation for any further information or to place an order.